www.technologieenindustrie.com
28
'12
Written on Modified on
Van zwakste schakel naar bewerkingssuperstar
Waarom nieuwe spindelverbinding zorgt voor maximale verspaning
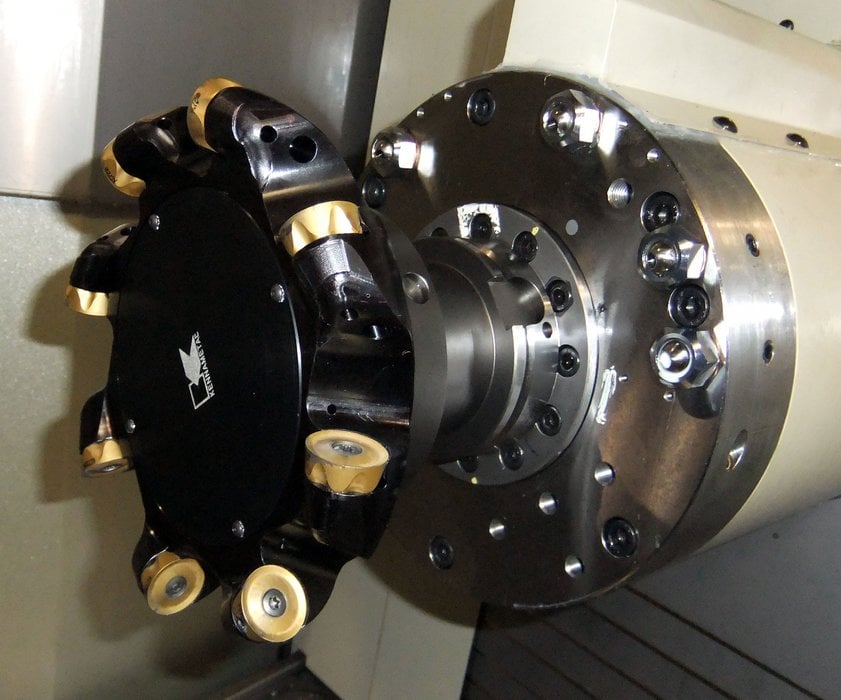
Mark Huston, Vice President, Global Engineered Solutions
Doug Ewald, Directeur, Global Product Management, Tooling Systems
Ruy de Frota de Souza, Manager, Global Tooling Systems, Product Engineering
Kennametal Inc, Latrobe, PA
Het bewerken van taaie materialen als titanium is een uitdaging op zich. Het bewerken van harde legeringen onder druk van het realiseren van een verbeterde productie-efficiency, betekent maximale verspaansnelheid bij lage snijsnelheden en grote snijkrachten. Gereedschapmachinebouwers hebben hierop gereageerd met speciale frezen en draaicentra met verbeterde spindelstijfheid en -demping en schaalbare machineconstructies, teneinde alle ongewenste trillingen te minimaliseren die de werkstukkwaliteit en de levensduur van het gereedschap ondermijnen. Hoewel deze verbeteringen hebben bijgedragen aan een grotere productiviteit, blijft het zwakste punt toch vaak de gereedschaphouder zelf.
In de meeste gevallen bepaalt de verbinding tussen machinespindel en snijgereedschap hoeveel materiaal kan worden verspaand bij een bepaalde bewerking. Dit komt omdat deze verbinding bestand moet zijn tegen hoge belastingen, zonder zijn stijfheid te verliezen, totdat de doorbuiging van het gereedschap te groot wordt of ‘chatter’ ontstaat. Met de voortdurende vooruitgang bij snijgereedschappen en bewerkingscentra, is een gereedschaphouder die het best gebruik maakt van de beschikbare capaciteit, aan het begin van de productieplanning het overwegen waard.
Verschillende typen gereedschaphouders zijn ontwikkeld of geoptimaliseerd in de afgelopen decennia. Door een goede kosten/baten positie, groeide de 7/24 ISO conus uit tot een van de meest populaire systemen in de markt. Het is een succes in vele toepassingen, maar nauwkeurigheid- en hogesnelheidsbeperkingen voorkomen verdere groei.
De opkomst van ‘face contact’ betekende een belangrijke stap ten opzichte van de standaard 7/24 conus. De combinatie van face contact met de 7/24 vaste conus biedt een hogere nauwkeurigheid in de Z-as richting, maar heeft tevens enkele nadelen, namelijk verlies van stijfheid bij hogere snelheden of hoge zijwaartse krachten. De meeste gereedschappen op de markt zijn vast en de spindels hebben een relatief lage klemkracht. De verbindingstijfheid is beperkt aangezien de radiale interferentie minimaal moet worden gehouden De vereiste toleranties om een consistent face contact te bereiken zijn dus zeer klein, wat leidt tot hoge productiekosten.
In 1985 startten Kennametal en Krupp WIDIA met een gezamenlijk programma voor de ontwikkeling van een universeel snelwisselgereedschapsysteem, nu bekend als KMTM en onlangs gestandaardiseerd volgens ISO 26622. In de vroege jaren ‘90 werd het HSK systeem in Europa toegepast op machines, later werd dit DIN 69893 en daarna ISO 12164.
Het KMTM snelwisselgereedschapsysteem bestaat uit twee basiscomponenten: de klemeenheid en de snijkop. De klemeenheid wordt op de machine gemonteerd (een revolverkop of gereedschapsblok voor stationaire toepassingen en een roterende spindel voor roterende toepassingen) en vormt het magazijn voor de verwisselbare snijunit/gereedschapshouder. Als een gereedschap moet worden verwisseld, ontgrendelt een operator simpelweg het vergrendelingsysteem, vervangt het snijgereedschap en vergrendelt dit weer in de juiste positie. Machinestilstand is hierbij een kwestie van seconden.
KM4XTM van Kennametal vertegenwoordigt de volgende generatie van KM. Bepaalde systemen zijn in staat om een behoorlijk groot koppel over te brengen, maar snijkrachten genereren ook buigmomenten, die de grenzen van de interface kunnen overschrijden voordat de koppellimieten worden bereikt. Door een combinatie van hoge spankrachten en geoptimaliseerde interferentieniveaus, zorgt de KM4X voor een robuuste verbinding, extreem hoge stijfheid en buigbelastbaarheid, resulterend in sterk verbeterde prestaties bij het bewerken van hogesterkte legeringen en andere materialen, bij extreem hoge verspaansnelheden en resulterend in meer gerede werkstukken per dag.
3x hogere buigweerstand
De gereedschaphouder moet zorgen voor voldoende koppel- en buigbelastbaarheid overeenkomstig de specificaties van de gereedschapmachine en de eisen voor hogere productiviteit. Dat wordt duidelijk bij eindfrees applicaties, waarbij projectielengtes doorgaans groter zijn en de beperkende factor de buigweerstand van de spindelinterface is. Neem bijvoorbeeld een indexeerbare helix frees met 250 mm (9,84 inch) projectie van het spindelvlak en een diameter van 80 mm (3,15 inch), deze genereert een buigmoment van 4620 Nm (3407,5 ft lbs.) en minder dan 900 Nm (663,8 ft lbs.) aan koppel bij het verspanen van 360 cm3/min van Ti6Al4V met een radiale snedebreedte van 12,7 mm en een Axiale snedebreedte van 63,5 mm. De meest kritische parameters van een conus spindelverbinding zijn de klemkracht en de radiale interferentie. Het maximaliseren van de klemkracht en het selecteren van de juiste interferentiewaarden kan de verbindingsstijfheid nog verder verbeteren. Het gebruik van ‘three surface contact’ voor een betere stabiliteit en optimale klemkrachtverdeling en interferentie, resulteert bij de KM4XTM techniek in een drie keer hogere buigweerstand in vergelijking met ander gereedschapsystemen.
Dit betekent:
- Werkplaatsen kunnen gebruikmaken van met KM4X uitgeruste high-performance machinegereedschappen om snelheden en voedingen te verhogen bij complexe bewerkingen, en zo het volledige productiviteitspotentieel van het gereedschap benutten.
- Vaak zal een kleinere KM4X verbinding, zoals een KM4X100 dezelfde of betere snijresultaten geven dan een grotere verbinding.
- KM4X systemen kunnen worden toegepast bij multi-tasking, draaibewerkingen, bewerkingscentra en transfermachines in de manuele, halfautomatische of volautomatische modus.
KM4X kan een breed scala van activiteiten uitvoeren, van lagesnelheid/hoogkoppel tot hogesnelheid/laagkoppel, waardoor producenten het maximale uit hun productieapparatuur kunnen halen.
Het frezen, boren en draaien van een breed scala aan materialen zorgt nu voor nog meer productiviteit!
Regels en aanbevelingen zijn van nature algemeen. Voor specifiek advies over het bewerken van titanium etc. op KM4X kunt u contact opnemen met Kennametal of een bezoek brengen aan www.kennametal.com
KM4X_with_cutter.jpeg: Door de combinatie van hoge spankrachten en geoptimaliseerde interferentieniveaus, zorgt KM4X voor een robuuste verbinding, extreem hoge stijfheid en buigweerstand voor sterk verbeterde prestaties bij het bewerken van hogesterktelegeringen en andere materialen, met een uiterst hoge verspaansnelheden en nog veel meer gerede onderdelen per dag.
KM4X_8.jpeg: Het KM4XTM spindelverbindingsysteem van Kennametal heeft een robuuste configuratie die kan zijn werk doen onder hogesnelheid/laagkoppel of lagesnelheid/hoogkoppel condities. Zonder KM4X zouden helix frezen als deze hun buigmomentlimiet overschrijden lang vóórdat de koppelgrenzen zijn bereikt.
KM4X_9.jpeg: Combinatie van oppervlaktecontact en klemkracht voor een betere interferentie en drie keer hogere buigweerstand in vergelijking met andere systemen. Het verwisselen van gereedschap is snel en eenvoudig en zorgt voor minimale machinestilstand.
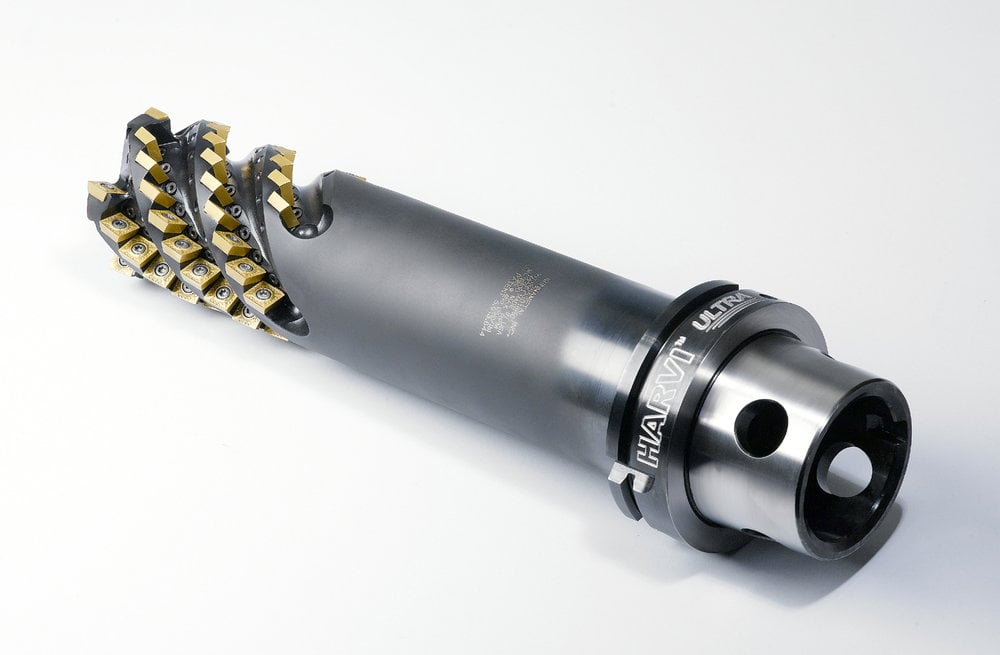
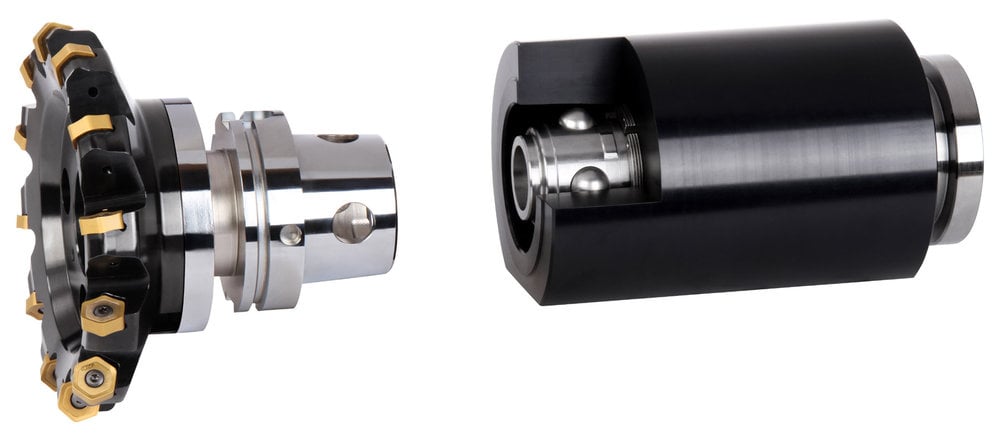