Laserline
Een sterke samenwerking
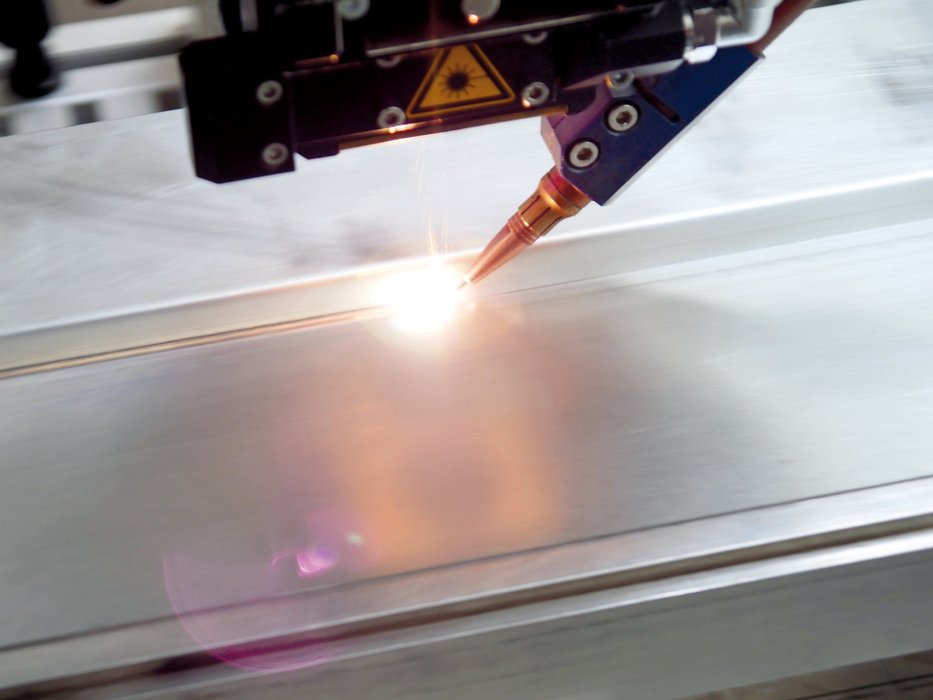
Laserstralen kunnen metalen zeer efficiënt en zeer nauwkeurig smelten, en zelfs verdampen. Daarom worden ze in toenemende mate gebruikt als hulpmiddel voor het verbinden van componenten, met name voor lassen en solderen, bijvoorbeeld in de automobielindustrie. Normaal gesproken hebben lasertoestellen - zoals gewone lastoortsen - één enkel brandpunt of "spot". Laserline heeft nu multispot-optiek ontwikkeld voor laser-solderen en -lassen, waardoor ook bijzonder moeilijke materialen kunnen worden verwerkt. Motoren van FAULHABER zorgen voor een correcte verdeling van de spot-energie.
Zink beschermt staal tegen roest. Voertuigfabrikanten gebruiken daarom voornamelijk verzinkt plaatstaal voor voertuigcarrosserieën. Vroeger werd de metalen beschermlaag door middel van galvanisering aangebracht. Thermisch verzinken als methode begint nu echter de voorkeur te krijgen. Dit biedt een nog betere bescherming tegen corrosie. Toen dergelijke thermisch verzinkte platen voor het eerst in productie werden genomen, ontstond er tijdens het solderen een onverwacht probleem.
Solderen of lassen?
In vergelijking met lassen biedt solderen een reeks voordelen voor serieproductie in de automobielindustrie. Bij het lassen worden de metaalplaten langs de lasnaad zelf tot smelttemperatuur verhit en worden de twee platen direct met elkaar verbonden. Dit vereist een hoge mate van precisie, en het is niet mogelijk om lassen van zichtkwaliteit te bereiken. Gelaste naden zijn ruw en door verdamping van zink zijn ze poreus. Bij het solderen wordt echter een naad van een ander materiaal als vulmateriaal tussen de metaalplaten geplaatst. Dit koper-siliciumsoldeersel - dat tijdens het solderen vloeibaar wordt en vervolgens weer stolt - voegt niet alleen de delen samen, maar vult ook de tussenruimte op. Hierdoor maakt solderen een grotere dimensionale tolerantie mogelijk en vergt het minder inspanning om de werkstukken te klemmen. Door solderen kunnen vooral spleetvrije verbindingen met zichtkwaliteit worden gemaakt, zodat de gesoldeerde componenten zonder verdere bewerking kunnen worden geschilderd.
Bij thermisch verzinkte metaalplaten gedraagt het soldeersel zich echter niet zoals gebruikelijk. "Op de oppervlakken naast de naad was er een verhoogd aantal spatten van vloeibaar soldeersel. Met name microspatten kwamen voor. Die zijn aanvankelijk moeilijk te zien, maar worden na het schilderen duidelijk zichtbaar," vertelt Dr. Axel Luft, Automotive Sales Manager bij Laserline. "Ook de kwaliteit van de naad zelf was verslechterd. Die was ruwer en vormde vaak zogenaamde golfjes, met andere woorden punten waarop het soldeersel de geplande naadgrens overschrijdt."
Soldeeroplossing voor thermisch verzinkte metaalplaten
Het was duidelijk dat deze problemen te maken hadden met de zinklaag op de metalen plaat. Door de thermische verzinking was deze laag dikker en minder regelmatig geworden. Bovendien vertoonde het een ander reflectiegedrag, wat ook een negatief effect had op het soldeerproces. Thorge Hammer, die als ingenieur bij Volkswagen in Wolfsburg op de afdeling voor technologische planning en ontwikkeling verantwoordelijk is voor dit soldeerproces, had een idee hoe dit probleem op te lossen: het zink moet van de randen van de naad worden verwijderd voordat men begint met solderen. Hiervoor zou echter de gebruikelijke cirkelvormige laserspot rechthoekig moeten zijn en ook een opening moeten hebben waardoor het soldeersel kan worden geleid. De "voorste" hoeken van de spot zouden dan verantwoordelijk zijn voor het verwijderen van het zink, terwijl het grootste deel van de rechthoek het eigenlijke solderen uitvoert.
"Technisch gezien was deze oplossing niet mogelijk, maar we waren op de goede weg," herinnert Dr. Markus Baumann, chief development engineer bij Laserline, zich. "In plaats van een spot te vormen met een complexe - en dus optisch zeer moeilijke - vorm, hebben we uiteindelijk twee kleinere spots aan de hoofdspot toegevoegd. Bij het solderen worden deze kleine spots altijd gericht op de randen van de naad enkele vierkante millimeters voor de hoofdspot uit." Hun energie is voldoende om de zinklaag in dit gebied te verdampen, het staal beginnen te smelten en lichte oxidatie te genereren. Hierdoor ontstaat een zogenaamde passieve laag die voorkomt dat het vloeibare soldeersel over de rand heen klotst.
De gesoldeerde delen hebben dus geen verdere bewerking nodig om spatten voor het schilderen te verwijderen. Er is nog een reden waarom de rechthoekige hoofdspot een goede oplossing bleek te zijn: hij verdeelt de warmte gelijkmatiger over het soldeersel dan zijn cirkelvormige tegenhanger, wat ook bijdraagt aan een rustiger soldeerbad. "Met deze technologie konden we eindelijk alle problemen oplossen die we tegenkwamen met thermisch verzinkte metaalplaten," zegt een tevreden Dr. Luft. "Het wordt nu gebruikt in de serieproductie bij VW. En het stelt ons in staat om een soldeersnelheid tot 4,5 meter per minuut te bereiken. Andere fabrikanten zullen spoedig volgen."
Straalscheiding met optische module
Een optische module zorgt voor een precieze uitlijning van de spots. Het bevat verschillende optische elementen die de laserstraal selectief wijzigen. De collimator zorgt ervoor dat de divergerende laserstralen die de optische vezelkabel verlaten parallel lopen aan elkaar. Een zogenaamde homogenisatiestraal genereert een vierkante hoofdspot, terwijl andere optische elementen de straal splitsen en extra spots genereren. In het geval van solderen worden twee spots voor en naast de hoofdspot gegenereerd. Om aan het einde van het proces de gewenste rechte naad te verkrijgen, moet de krachtverdeling tussen de hoofd- en vooropgaande spots en tussen de vooropgaande spots onderling precies worden ingesteld. Hoe het laservermogen over deze spots wordt verdeeld, is afhankelijk van de positie van de optische elementen. Door deze elementen langs de x- en de y-as te verplaatsen, is het mogelijk om de exacte verdeling van het laservermogen te bereiken die nodig is voor de taak in kwestie.
Om bijvoorbeeld aluminium diep te lassen kan een kleine, intensieve spot in de zwakkere grote spot worden geplaatst. Om metaalplaten van verschillende diktes aan elkaar te lassen, kunnen de twee spots aangepast worden aan hun respectievelijke materiaal. Dit kan gedurende het proces zelf gebeuren, omdat de elementen in de Laserline optische module door motoren worden bewogen.
De randlengte van deze vierkante module is 12 centimeter, met een diepte van 5 centimeter. In deze kleine ruimte zijn de optische elementen en een verfijnd mechanisch systeem ondergebracht. Er is niet veel ruimte over voor de motoren. De belangrijkste vereiste voor de aandrijving is dan ook compactheid.
"Wij hebben gekozen voor borstelloze DC-servomotoren uit de 1226 B FAULHABER serie met een diameter van 12 millimeter, met direct op de motoras aangebrachte geleideschroeven en zonder askoppeling," legt Dr. Baumann uit. "Hierdoor hebben we een zeer compacte aandrijving, die toch betrouwbaar het benodigde vermogen en toerental levert. Makkelijke integratie van de motorregelaar in het systeem was een andere belangrijke overweging." De Motion Controller van FAULHABER werd buiten de module geplaatst; de communicatie verloopt via een RS232 seriële interface. Op verzoek van de Laserline-klant kan de combinatie van motor en controller ook via een CAN-bussysteem worden aangestuurd, zonder dat hiervoor wijzigingen in de mechanica of behuizing vereist zijn. De RS232-controller kan eenvoudig worden vervangen door een uitvoering met CANopen-interface.
Motor met positiegarantie
De laseroptiek wordt tijdens het solderen en lassen op een robotarm gemonteerd; deze robotarm brengt de laseroptiek in de gewenste positie. De optiek moet bestand zijn tegen aanzienlijke dynamische belastingen die op de motoren inwerken en die ongewenste positieveranderingen kunnen veroorzaken. "Dit is geen probleem voor de FAULHABER-motor, omdat deze met de geïntegreerde Hall-sensor de actuele positie detecteert en indien nodig bijstelt - uiterlijk wanneer de laser op de naad wordt geplaatst," benadrukt Dr. Luft. "Dit geeft ons de zekerheid dat onjuiste positionering is uitgesloten. Dankzij de hoge kwaliteit van de schijven kunnen we vertrouwen op consistent reproduceerbare resultaten. Dit is cruciaal, want onze klanten verwachten ten minste zeven jaar lang probleemloze werking!"
Voor Dr. Baumann was het duidelijk dat hij bij FAULHABER de juiste motor zou vinden - net als acht jaar geleden toen hij op zoek was naar de juiste motor voor een nieuw zoomoptiek-systeem. In die tijd werden stappenmotoren over het algemeen gebruikt voor dit type apparaat. Deze stappenmotoren hadden echter problemen met de acceleratie van massa's in de robotarm, zoals de ontwikkelaar rapporteert: "De dynamische belasting kan ertoe leiden dat een stappenmotor afzonderlijke stappen mist. Om dit te voorkomen kan een encoder aanvullend worden gebruikt voor positiebepaling en -aanpassing. Dit is niet alleen ingewikkeld, maar in deze combinatie is het ook duur. Toen ik jonger was, had ik een compacte motor nodig voor een modelschip en die vond ik bij FAULHABER. Ik herinnerde me dit bij de ontwikkeling van het zoomoptiek-systeem, nam contact op met FAULHABER en vond opnieuw de optimale aandrijving. Dit heeft ons geholpen om een uiterst kosteneffectieve oplossing te creëren die sindsdien zeer succesvol is gebleken." Ook de nieuwe multispot-module voert zijn werkzaamheden in serieproductie vlekkeloos uit. Bovendien heeft dit optische systeem al een brede erkenning gekregen onder deskundigen: de technische oplossing en de economische efficiëntie die in korte tijd werd bereikt in industriële toepassingen overtuigden de internationale jury van de "Innovation Award Laser Technology". Dit jaar gaf het de eerste prijs aan het ontwikkelteam.
www.faulhaber.com