www.technologieenindustrie.com
31
'19
Written on Modified on
Data zijn het nieuwe goud
Atlas Copco Tools heeft zijn Smart Factory-visie consequent doorontwikkeld. In september 2019 hield het bedrijf zijn roadshow "Smart Connected Assembly – Powered by Data", met 44 evenementen waarop het liet zien hoe de complete productie op een nieuw, hoger niveau kan worden gebracht. Data kunnen op een intelligente manier worden geregistreerd, geanalyseerd en benut, en dat geeft Industrie 4.0 vleugels voor de toekomst.
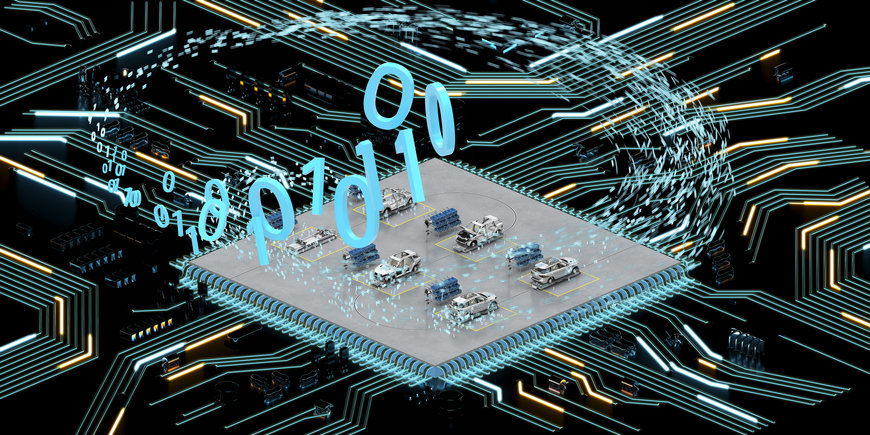
In positieve zin." Henning Appiß, businessmanager Software bij Atlas Copco Tools, ziet dat er een enorm belangrijke trend gaande is: steeds meer producenten willen optimaal gebruik maken van de data die binnen hun productie wordt gegenereerd. De markt wordt steeds internationaler en bedrijven willen daarom hun wereldwijde processen optimaliseren, de kwaliteit nog beter garanderen of profiteren van service en onderhoud op maat. "De grootste kansen qua toegevoegde waarde liggen op het gebied van de montage, maar bedrijven hebben vaak niet de operationele analysefuncties in huis om alle data die samenkomen zodanig in de bedrijfsprocessen te integreren dat het winst oplevert", heeft Appiß uit talrijke gesprekken ervaren.
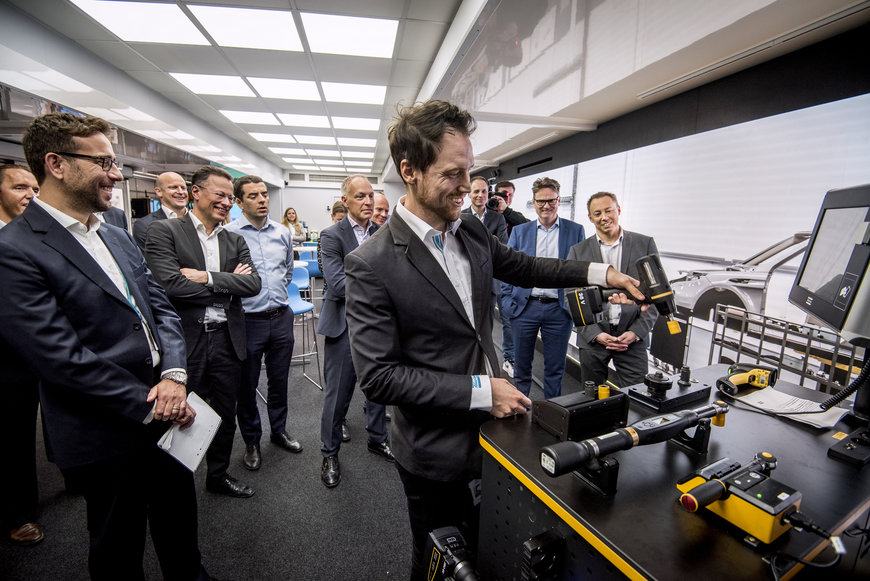
Goudkoorts ten tijde van de vierde industriële revolutie: montagedata verzamelen, analyseren en omzetten in geoptimaliseerde processen, een betere ergonomie en meer efficiëntie. De Roadshow Smart Connected Assembly – Powered by Data laat het potentieel zien van intelligent genetwerkte montagesystemen.
`Roadshow 2.0’
Daarom begon Atlas Copco Tools na het succesvolle debuut van vorig jaar aan zijn tweede grote roadshow over Smart Connected Assembly (SCA). De ondertitel was 'Powered by Data' en in de evenementenreeks werd dan ook een datagestuurd totaalconcept gepresenteerd, dat veel verder ging dan het Industrie 4.0-concept voor schroeftechniek uit 2018. In september werd het volledige portfolio voor verbindingstechniek in de vierde industriële revolutie uitgerold, samen met zusterbedrijf Atlas Copco Industrial Assembly Solutions (IAS).
Wie een bezoek bracht aan de 38 ton zware beursmobiel, kreeg diepgaande inzichten in de slimme montagewereld van de toekomst. Daarin genereren de intelligente gereedschappen en oplossingen van Atlas Copco continu data, die met behulp van Data Analytics en Machine Learning worden geanalyseerd en benut.
“ De intelligente installaties en gereedschappen van Atlas Copco genereren in elke productiestap en productiefase data via hun geïntegreerde sensoren. Via het netwerk kunnen we die vervolgens allemaal samenvoegen en analyseren. Daarna kunnen we ze meerdere keren gebruiken om specifieke processen te verbeteren of om Data Driven Services op maat te bieden. Zo zorgen we voor continue optimalisatie. ”
Henning Appiß , businessmanager Software, Atlas Copco Tools
Honderden bezoekers uit België, Nederland en het Duitstalig gebied wilden daar graag meer over weten en kwamen langs bij de in totaal 44 brancheoverschrijdende evenementen op 17 locaties. Ze maakten daar dankbaar gebruik van de mogelijkheid om intensieve gesprekken te voeren met vakmensen en lieten zich inspireren door het enorme economische potentieel dat – vooralsnog onbenut – schuilt in onbewerkte productiedata.
“ Ik vind het heel interessant om te zien hoe digitale data verzameld, geanalyseerd en gebruikt kunnen worden om de productie verder vooruit te helpen. ”
Lambert Schmidt , productieplanner, Evobus Mannheim
Continue verbetering
"Smart Connected Assembly is een technologie die gedurende de hele levenscyclus van een product data verzamelt, analyseert en bruikbaar maakt." Volgens Appiß is het SCA-concept een perfecte, harmonieuze cyclus. Daarin grijpen de ontwikkeling, de prototypebouw, de serieproductie, de nabewerkingen en het onderhoud naadloos in elkaar. "Er zijn simpelweg geen geïsoleerde onderdelen meer; elk segment profiteert van de verbeteringen in andere segmenten."
Samen ontwikkelprocessen vormgeven
Een duurzame productie begint al in de planningsfase. Ieder product dat ooit geproduceerd wordt, begint bij het ontwerp. Lang voor de daadwerkelijke productie – die vaak ook op een andere locatie plaatsvindt – kunnen er al gegevens worden verzameld die kunnen helpen in het klantproces. Zo kan Atlas Copco bijvoorbeeld bepalen welke werkwijze het meest productief of ergonomisch is voor een bepaald soort verbinding en in realtime kijken hoe soortgelijke componenten en materialen zich daadwerkelijk gedragen. Allemaal nog voordat het eerste prototype is gebouwd. Onze digital twin in het Tech Center van de fabrikant of in ons Innovation Center bij IAS in Bretten definieert het product ondertussen tot op het punt waarop we samen met de ontwikkelaars van onze klanten toegankelijkheidstests kunnen doen, aanpassingen kunnen voorstellen en concrete complexe beproevingen kunnen uitvoeren."
Een flexibelere prototypebouw
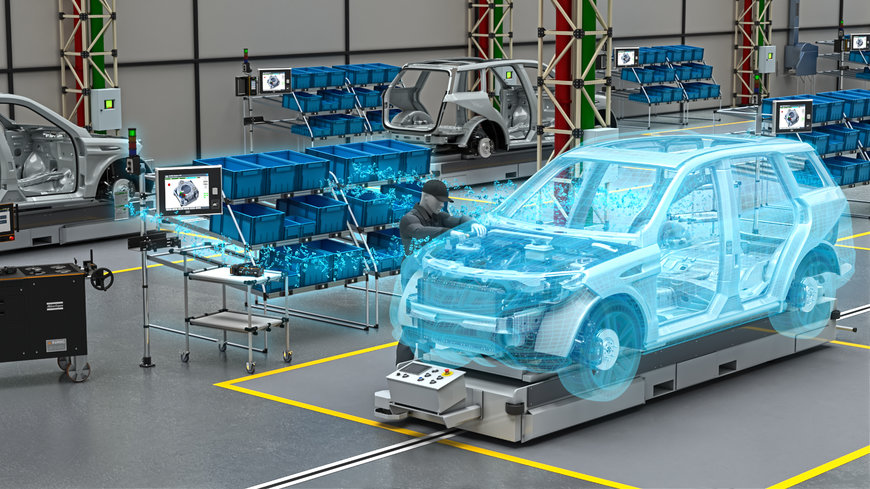
Op het prototypestation komen de digitale data van de digital twin en de fysieke hardware samen. Gedraagt een verbinding zich in de praktijk zoals de ontwikkelaars het hebben voorspeld? Komen eventuele zettingsverschijnselen bij een bepaalde aanhaalwijze overeen met de waarden die vooraf zijn berekend?
Bij het prototype blijkt of alle aannames correct zijn. De gereedschappen en strategieën worden gevalideerd en waar nodig aangepast, en de werkstappen tijdens de serieproductie worden
vastgelegd. "Niet elk gereedschap is geschikt voor elke verbinding. Maar door data en daden te combineren, kunnen we op het prototypestation alle componenten en stappen testen, de processen vormgeven en waar nodig aanpassingen doen. Alleen al daarom registreren we ook tijdens het prototypestadium alle waardevolle datasets in een gezamenlijke database, waarna we ze kunnen analyseren en kunnen benutten in andere onderdelen van de productie."
Juist bij wereldwijd opererende bedrijven is het heel belangrijk dat er over de hele wereld volgens uniforme standaarden wordt geproduceerd. Deze standaarden kunnen hier optimaal worden gedefinieerd en na goedkeuring met één druk op de knop worden verstuurd naar alle vestigingen.
Geavanceerd datagebruik versnelt de processen voor voorseries en verlaagt de kosten, zodat de standaardproductie eerder kan beginnen. Alle gegevens en alle voorschriften worden op een efficiënte manier naar alle locaties binnen de productielijnen gestuurd – in de vorm van data, zodat er niet meer van medium hoeft te worden gewisseld.
Optimalisatie van de serieproductie
In de moderne serieproductie wordt er tegenwoordig vaker gebruik gemaakt van alternatieve verbindingsprocessen. Zo worden in de voertuigbouw de schroeftechniek en het klassieke puntlassen van staal aangevuld met nieuwe technologieën en materialen. Bepaalde structuren en gewichtsverlagingen zijn, als de stabiliteit hetzelfde moet blijven, vaak alleen mogelijk als er meer onderdelen worden verlijmd of als het verbinden plaatsvindt via stansnieten of vloeiboorschroeven.
Atlas Copco heeft deze moderne werkwijzen in zijn portfolio zitten en maakt ze compleet met optische systemen voor geautomatiseerde, visuele kwaliteitsbewaking. In de virtuele bodyshop in de showtruck konden bezoekers op indrukwekkende wijze zien hoe de hybride verbindingswijzen worden toegepast in de carrosseriebouw, met een hoge mate van automatisering. Ook was, aan de hand van de productie van een echte stoel, te zien hoe de data uit het prototypestation in de praktijk worden weergegeven. Hier wordt de medewerker op een veilige manier door het productieproces geleid via zogeheten Error Proofing. Dit systeem stuurt de afzonderlijke stappen aan en maakt zodoende een poka-yokeproces mogelijk dat fouten meteen herkent en voorkomt via technische preventievoorzieningen.
Wereldwijd gestandaardiseerde processen
"We kunnen onze uitgebreide kennis over de toepassing uit de schroeftechniek ook toepassen op de andere verbindingstechnieken. Door data vanuit de design- en prototypefase te importeren in de serieproductie en ze daar te analyseren, kunnen we voor vrijwel alle materiaalkoppels het beste verbindingssysteem aanbieden", zo herhaalt Appiß zijn credo: data verzamelen, analyseren en bruikbaar maken. Volgens hem kan Smart Connected Assembly in alle productietakken eventuele kwaliteitsproblemen vroegtijdig herkennen, potentiële besparingen bepalen en zorgen dat het betreffende proces technisch optimaal en zo efficiënt mogelijk wordt uitgevoerd.
"Door centraal, datagestuurd productiemanagement maken we een wereldwijde implementatie van gestandaardiseerde processen mogelijk. Internationale producenten kunnen in elke vestiging ter wereld produceren in dezelfde hoge kwaliteit, volgens uniforme standaarden. En mocht er tijdens de montage toch een keer een fout optreden, dan kan meteen het reparatie- of nabewerkingsproces worden opgestart. Alle systemen zijn met elkaar verbonden en versturen de betreffende gegevens in realtime naar elke gewenste plek op de wereld."
Minder nabewerkingen
Achter veel productielijnen staat vaak een nabewerkingsstation, waar foutieve onderdelen naartoe worden gesluisd zodat eventuele schade kan worden verholpen. Hier maakt SCA aanzienlijke verbeteringen mogelijk, omdat de digital twin het nabewerkingsstation nauwgezet informeert over elk product. De producthistorie met alle eerdere stappen komt in beeld, net als alle geregistreerde meet- en aanhaalwaarden. Dat maakt het mogelijk om heel gericht correcties uit te voeren zonder eindeloos te moeten zoeken. En dat bespaart weer werkzaamheden én kosten. Ook bij de nabewerkingsprocessen worden alle relevante data verzameld, geanalyseerd en bruikbaar gemaakt.
Binnen de SCA-filosofie heeft men ook werkwijze voor ogen waarbij de montage meteen goed verloopt, doordat eventuele correcties meteen op het montagestation worden uitgevoerd. "Bij de roadshow hebben we de 'First Time Right'-werkwijze laten zien. Idealiter gaat die manier van werken nabewerkingsstations op de lange termijn overbodig maken", voorspelt Henning Appiß.
Intelligent onderhoud met Data Driven Services
Het SCA-concept heeft ook grote gevolgen voor de factor service, waarvan het belang in de toekomst nog verder zal groeien. Datagestuurde analyses laten zien welk optimalisatiepotentieel er ligt op het gebied van onderhoud, met betrekking tot schroefprocessen en zelfs bij de gerichte kwalificatie van medewerkers.
Productievoorzieningen, controllers en gereedschappen sturen continu en in realtime productiedata. Deze worden geanalyseerd en geïnterpreteerd zodat een service-app vroegtijdig kan laten zien dat er actie nodig is. "Het dashboard van deze app maakt de toestand van de productiemiddelen volledig transparant, en data-analyses op basis van 'Machine Learning' bevrijden producenten van vaste onderhoudsintervallen. Productie- en onderhoudsmanagers krijgen bij trends of afwijkingen meteen bericht.
“ De communicatiemogelijkheden in Industrie 4.0 zijn voor ons heel interessant en kunnen ons helpen om de kwaliteit van onze productie in de toekomst nog verder te verbeteren. ”
Axel Hoff , werkvoorbereiding, Nord-Micro GmbH & Co. OHG, Frankfurt
Kwaliteitsbewaking 4.0
Voor de afdelingen Kwaliteitsbewaking in de industrie gaat er door de intensievere verzameling en analyse van data eveneens een wereld aan nieuwe mogelijkheden open. Met het Quality Assurance-platform dat op de roadshow werd vertoond, worden de kwaliteitsprocessen onderdeel van de intelligent genetwerkte montage. Medewerkers worden in vastgelegde stappen door de testprocedures geleid en daarnaast wordt het risico op menselijke invoerfouten uitgebannen, iets wat bij testlijsten of Exceltabellen altijd op de loer ligt.
Networked mounting system = limitless profit
Atlas Copco ensures that data collected early can be used again and again and that software and hardware can work together more closely at all levels. As a strategic partner, Atlas Copco thus delivers measurable added value for its customers. Henning Appiß sees the real key to Industry 4.0's success in collecting and analyzing all available information in a data center. "This advanced data usage is not the ultimate goal for the assembly world; it is the first step to the future!"
www.atlascopco.com