www.technologieenindustrie.com
14
'20
Written on Modified on
Procestransparantie inbegrepen
Conditiebewakingssystemen (CMS) detecteren veranderingen en afwijkingen in het productieproces. Ze geven een vroege waarschuwing voor beginnende schade, detecteren afwijkingen in kwaliteit, bewaken de stabiliteit van een productieproces en zorgen voor consistente kwaliteitscontrole bij alle fases van de productie en waardecreatie. In deze context worden grijpsystemen en kleminrichtingen steeds belangrijker door hun closest-to-the-part-positie.
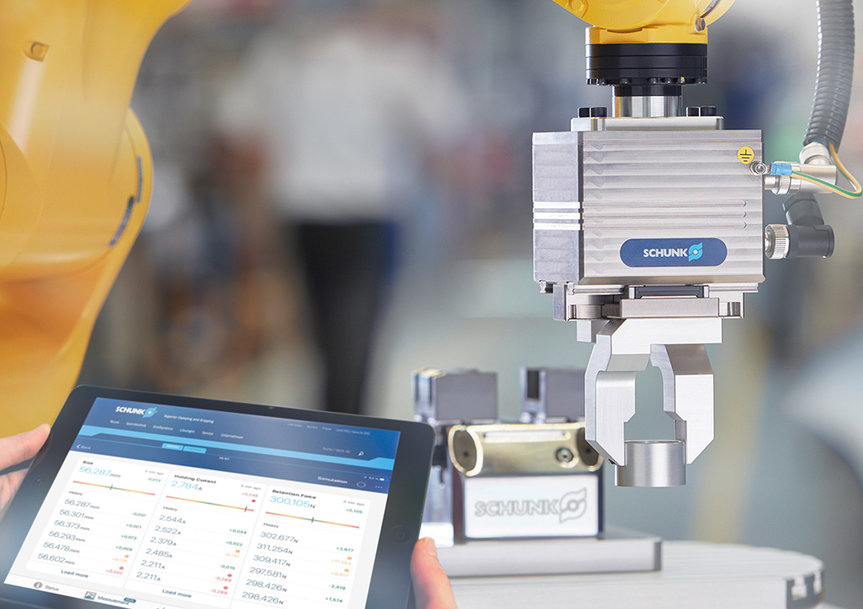
De vraag van gebruikers naar hogere productiviteit, geautomatiseerde systeembeschikbaarheid en procesbetrouwbaarheid heeft een impact op de machines en geautomatiseerde systemen die worden gebruikt in de moderne productie. Steeds meer wordt de mogelijkheid om continue conditiemonitoring uit te voeren een belangrijk criterium bij de selectie van componenten. De mogelijkheid om productie- en kwaliteitsgegevens te analyseren in gelijke tred met de productie kan zorgen voor aanzienlijke kostenbesparingen, hogere operationele efficiëntie en verbeterde productiekwaliteit.
Het is aangetoond dat vooral de hogere beschikbaarheid van geautomatiseerde systemen en een Just-in-Time-Maintenance de operationele efficiëntie verbetert. In het ideale geval kunnen ongeplande uitvaltijden voor geautomatiseerde systemen volledig worden weggewerkt. Op zijn beurt kan de productkwaliteit worden verbeterd door gegevens over de slijtage aan de machine in de procesbesturing op te nemen en door afwijkingen van standaard kwaliteitsmaatregelen te voorspellen, zodat alle noodzakelijke acties tijdig kunnen worden ondernomen.
Niet alleen gegevens lezen, maar ook gegevens analyseren
Vandaag al produceren machines en geautomatiseerde systemen, slimme gereedschappen en componenten in fabrieken van productiebedrijven enorme hoeveelheden gegevens. Slechts een zeer klein deel van deze gegevens wordt echter werkelijk gebruikt - volgens schattingen is dit slechts ongeveer vijf procent. Er werd tot nu toe weinig belang gehecht aan de door de sensoren geregistreerde waarden en ze worden hooguit in geval van schade of voor het oplossen van problemen gebruikt. Door deze bestaande gegevens volledig, systematisch en vooral in realtime te gebruiken, kunnen slimme productiescenario's worden gerealiseerd die enorme voordelen beloven.
Bovendien gaat de stijgende netwerkintegratie en digitalisering ook gepaard met een snelle toename van de hoeveelheid gegevens die wordt gegenereerd, wat betekent dat er een risico bestaat dat de verbindingen met de cloud-datacenters mogelijk niet in staat zijn om de enorme en snel groeiende datastromen aan te kunnen, en dat uitvaltijden en hoge latentieperioden kunnen optreden. Daarom richten huidige onderzoeksprojecten zich op een fundamentele verandering in de manier waarop gegevens worden begrepen. Het draait niet langer alleen om het verzamelen van gegevens zoals eerder het geval was, maar om ze al ter plaatse te analyseren en om te zetten in waardevolle informatie. Centraal staat de vraag hoe Big Data kan worden omgezet in Smart Data. Gevraagd wordt bijv. gegenereerde informatie waarmee kan worden nagegaan of een geautomatiseerd systeem correct functioneert en die in het ideale geval is gelinkt aan de nodige aanbevolen acties.
Geïntegreerde test van componenten
Hierdoor kunnen de kwaliteitskenmerken van componenten worden gecontroleerd tijdens de handling en OK/NOK-beslissingen gebeuren direct in de grijper. De in de grijper geregistreerde gegevens worden direct in de componenten in realtime voorbereid en geanalyseerd om de nodige reacties te activeren. Hierdoor wordt het datavolume dat moet worden overgedragen, beperkt tot het nodige.
Dit betekent dat een enigszins verbijsterende hoeveelheid gegevens als betekenisvolle parameters of key performance indicators (KPI's) wordt gekanaliseerd. Naast standaard downtime-statistieken zijn de belangrijkste KPI's de vermogenskarakteristieken van het proces (Cp) uit de statistische procesanalyse en de gebruiksefficiëntie van het totale geautomatiseerde systeem. Deze meet drie soorten prestatiegegevens en maakt gebruik van multiplicatieve methoden om ze samen te voegen tot een uitgebreide productiviteitsindicator, de totale efficiëntie van het geautomatiseerde systeem of de Overall Equipment Effectiveness (OEE).
www.schunk.com